¶ PCB Revisions and schematics
This section outlies the various PCB versions that have been in development during this project, as well as what features the boards add. It is recommended to use the latest PCB design if you are building the TCU yourself.
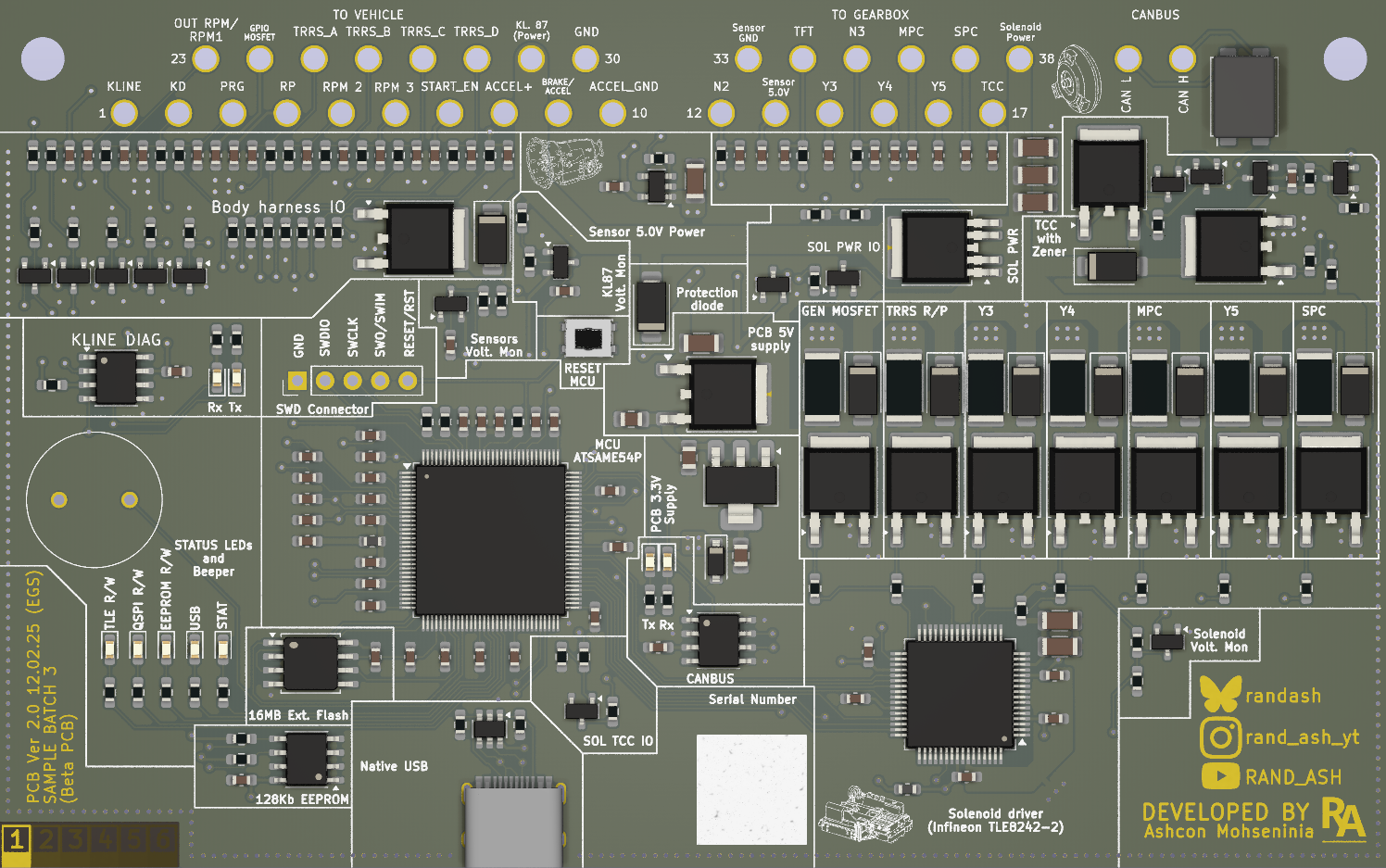 |
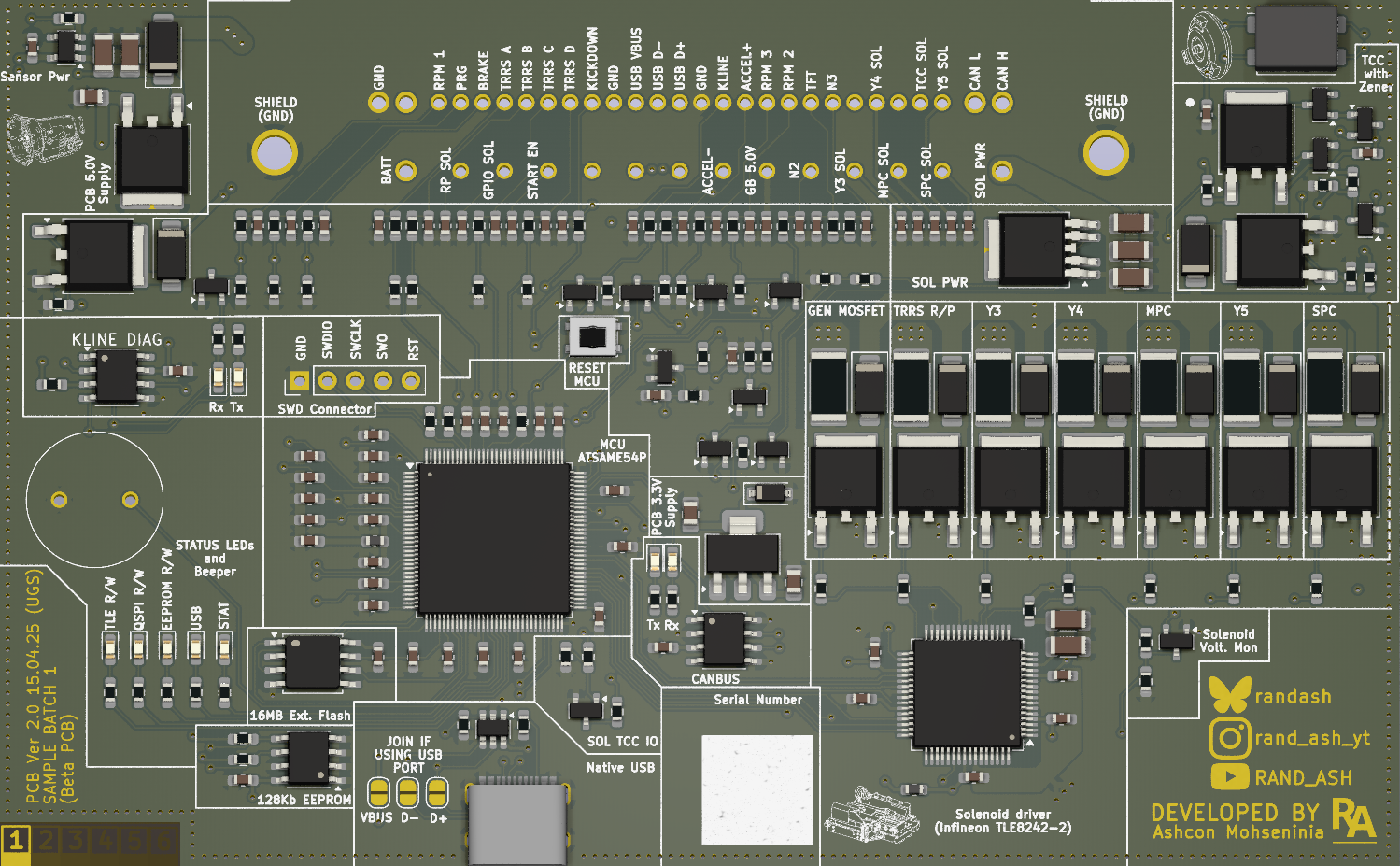 |
EGS Variant |
UGS Variant |
- Upgraded specs
- Replaced ESP32 with ATSAME54P/PIC32CX automotive-grade processor
- Infineon TLE8242-2 for solenoid control and error detection
- 16MB external QSPI flash
- 128KB dedicated EEPROM
- 6 layer PCB
- Native USB - No more UART
- Firmware flashing via bootloader (USB/CAN/KLINE), or SWD (Debug header)
- Firmware written from the ground-up in Rust
- TCC Zener circuit built-in
- Add K-Line for diagnostics
- High side power switch for solenoid power (Emergency shut off)
- Conductor plate power supply monitoring and emergency shut off
- Separate to PCB 5.0V supply so that it does not affect the PCB
- Bigger CAN Choke (Stronger connection to PCB)
- 3x RPM sensors on the PCB (0-12V input)
- Add accelerator pedal input (Potentiometer input)
- UGS variant (Universal) with an upgraded connector and support for USB via the main wiring harness rather than the USB port
- TRRS R/P solenoid and GPIO MOSFET output controlled by TLE8242 (For error detection)
- Add dedicated HGS Variant (UN52-HGS) with a much better connector
- Switch polarity of kickdown switch
- Remove the USB-C port, and expose the USB connection via the connector harness
- Expose extra pins of GPIO expander via the connector
- Emergency solenoid high side power cutoff
- Conductor plate sensor power supply monitoring
- Conductor plate sensor power supply shut off
- Solenoid voltage supply monitoring
- Quad layer PCB
- Switch from space-consuming TPS Buck converter regulators to space-saving LDOs
- Increase size of CAN Filter, to prevent it being easily knocked off the PCB
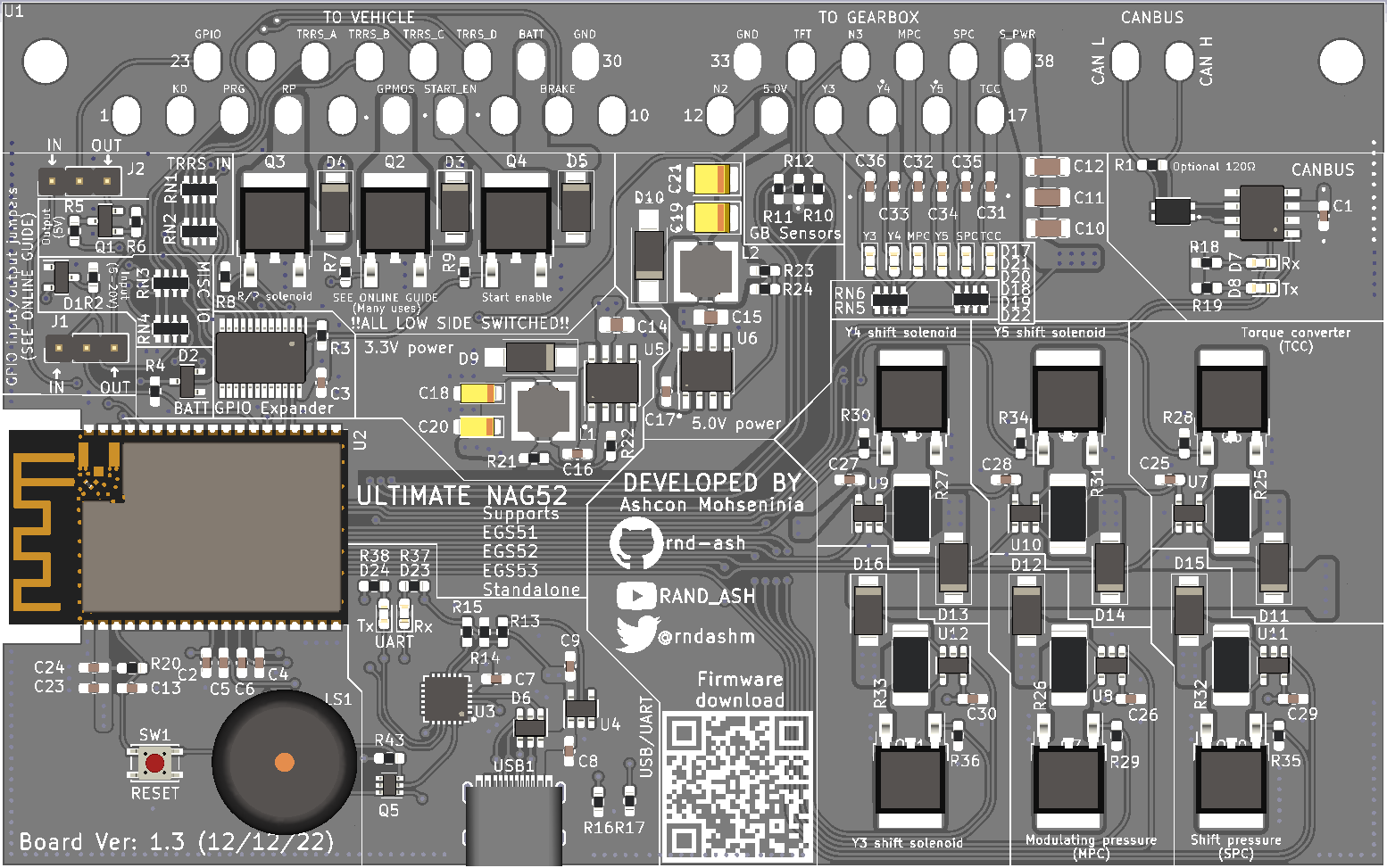
- Switched all basic SMD components (Capacitors and resistors), for higher temperature rated ones, in order to better handle engine bay installations
- Added LEDs for CAN, UART and Solenoids
- Added general purpose N-channel MOSFET on pin 6
- Added multi-use IO for pin 23 (Allows for reading G-class' output shaft sensor, or driving a speed sensor in some W124 applications)
- Added QR code on PCB silkscreen for firmware download link
¶ Schematic and build files
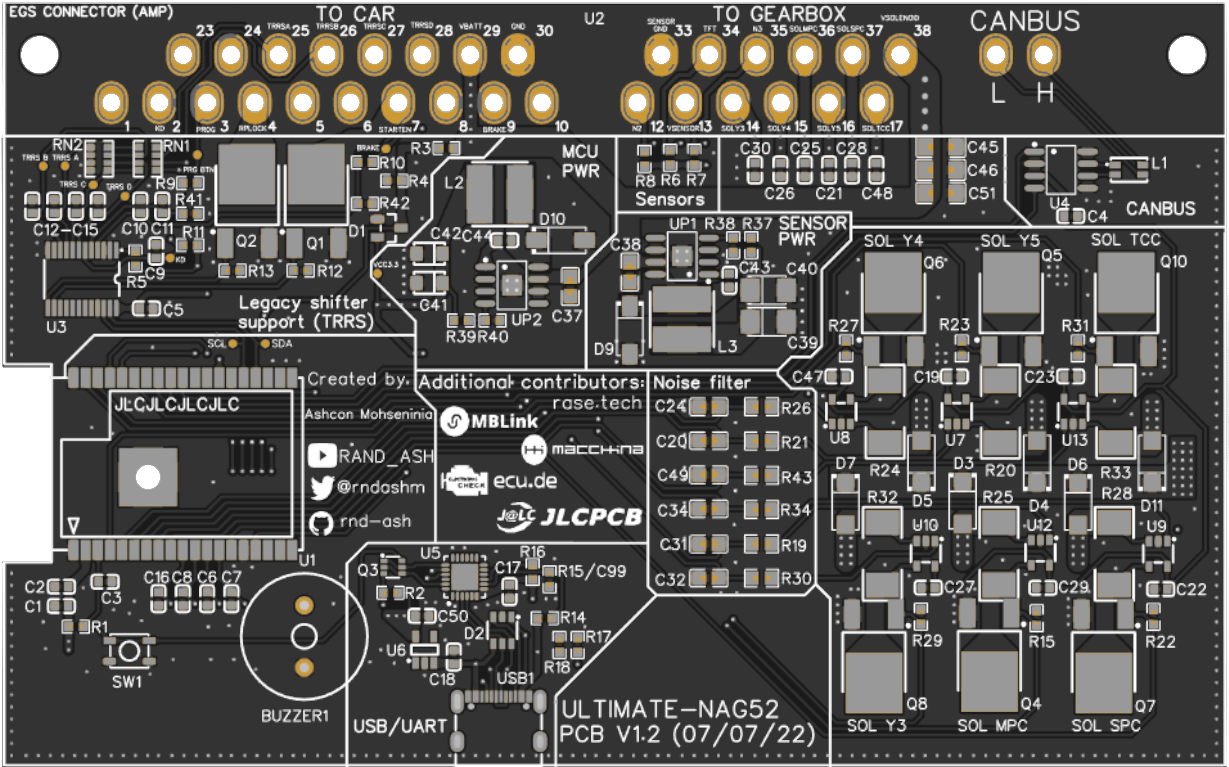
- Added legacy shifter support. This adds support for W210 generation of vehicles, and some early cars built from 2000. This includes a GPIO expander which reads data from the TRRS data lines, the Kick-down, Brake and Program button inputs, and outputs for start enable and R/P shifter solenoid.
- Switch CP2104 for CP2102 UART bridge
- Add ESD Diode to PCB
- Switched buck converters to more modern circuity
- Removed all electrolytic capacitors in favour of Tantalum ones
¶ Schematic and build files
Capacitors C20, C24, C31, C32, C34, and C49 must be removed! (Found to make current monitoring worse)
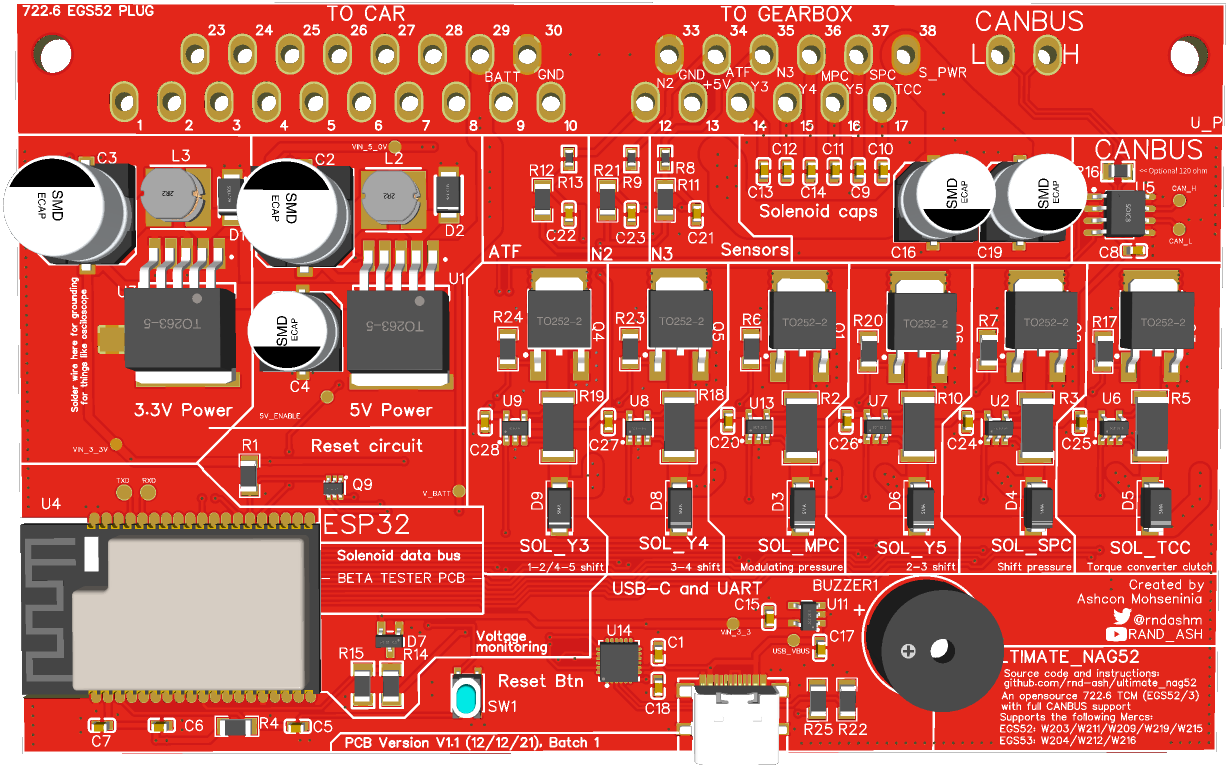
- Initial PCB made publicly available for testing
¶ Schematic and build files